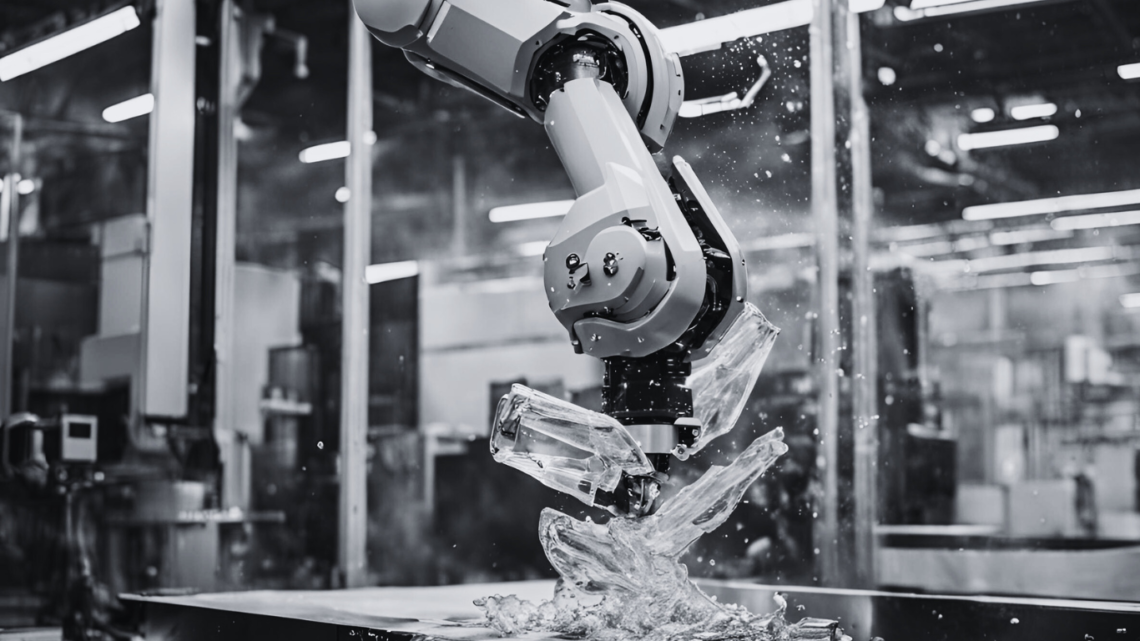
Commento a “Oltre la produzione snella” di Kim Moody
In più passaggi Moody insiste su un presunto calo della produttività. (“La produttività manifatturiera negli Stati uniti è aumentata di circa il 4% all’anno fino alla Grande recessione del 2008-2010. Ma poi è crollata. […] L’aumento annuale della produttività manifatturiera è stato rimandato al 2019. È aumentato di nuovo nel 2021 con l’attenuarsi della pandemia, per poi diminuire nuovamente nel 2022 e nel 2023”). A supporto di questa affermazione non ci sono dati: per quanto mi riguarda nei pochi casi in cui la produttività è misurabile in termini fisici (seppur anche qui ci sarebbero da fare alcune precisazioni), essa risulta tutt’altro che in calo, anzi!
Una domanda sorge spontanea: la produttività citata da Moody come viene misurata? Il tema non è una questione tecnica, ma politica. La risposta – almeno in parte, non voglio forzare le sue parole – la troviamo poco dopo, quando menziona la “produttività multifattoriale”, in sostanza la Produttività Totale dei Fattori, un concetto chiaramente neoclassico, il cui calcolo si basa sulla funzione di produzione. Un concetto dal quale dovrebbe tenersi ben distante chiunque intenda collocarsi in un versante ben preciso della lotta di classe.
Attribuire un presunto abbandono del modello Lean a un altrettanto presunto calo della produttività non appare fondato. Ripeto, sulla base di quali dati?
Lo stesso dicasi a proposito di un presunto fallimento delle tecnologie (che in questo caso l’autore limita alla robotizzazione e automazione) nell’incrementare l’output per lavoratore. Se il riferimento dell’autore è allo studio redatto per l’International Labour Organization di Pardi, Krzywdzinski e Boy negli stabilimenti di assemblaggio auto di alcuni Paesi, il quadro descritto dai tre ricercatori è un po’ più complesso della sintetica affermazione di Moody a proposito di un totale fallimento di questa strategia aziendale che ne avrebbe giustificato il suo abbandono. I tre ricercatori, infatti, riconoscono che dopo una grande ondata di robotizzazione/automazione, nella seconda parte degli anni Novanta i carmakers hanno fortemente rallentato questi investimenti e che nei due decenni successivi gli stock di robot industriali negli stabilimenti di assemblaggio auto hanno tendenzialmente ristagnato: in essi il tasso medio di automazione non si è incrementato e in alcuni casi è diminuito. Ma è altrettanto vero che i tre autori espongono una serie di aspetti, due dei quali è utile menzionare. Il primo, manifestatosi già nelle prime fasi di questa automazione, è riferito ai problemi dei frequenti fermi-macchina e alla bassa flessibilità di questi impianti, che obbligava a rallentare l’introduzione di nuovi modelli. Il secondo, in parte legato al primo, è riferito al fatto che, negli anni scorsi, l’eventuale ulteriore diffusione dell’automazione negli stabilimenti di assemblaggio auto dipendeva dalla riduzione delle varianti del prodotto, mentre negli anni 2000 e 2010 è avvenuto l’esatto contrario, ossia l’incremento della variabilità e della complessità del prodotto da realizzare.
Ecco che i due aspetti del lavoro dell’ILO chiamano in causa un ulteriore aspetto tecnologico, quello di Industria 4.0, tra le cui finalità vi sono appunto quelle di risolvere quei problemi che limitavano le potenzialità dell’automazione industriale. L’equipaggiamento dei macchinari con sensori diffusi e connessi, in grado di registrare in continuo e in tempo reale il funzionamento di un macchinario, e con sistemi ICT in grado di raccogliere questi dati per trasmetterli a unità logiche – siano esse personal computer a bordo macchina o direttamente localizzate negli uffici deputati al controllo del processo produttivo – per renderli immediatamente visibili, dovrebbe appunto consentire di anticipare guasti e fermi-macchina, anche attraverso forme di manutenzione preventiva. Non è un caso che larga parte delle tecnologie 4.0 si siano appunto diffuse nell’ambito della manutenzione degli impianti industriali, proprio per garantirne il funzionamento continuo, senza interruzioni o rallentamenti. Dall’altra parte, le tecnologie 4.0, si propongono anche l’obiettivo di rendere sempre più flessibili i macchinari, intervenendo sui programmi di funzionamento in modo da ridurre al minimo i tempi di riattrezzaggio delle macchine, di nuovo set-up dei parametri operativi ecc., aspetti tipici dei lotti variabili o della variabilità dello stesso prodotto. Inoltre è ovvio che non tutte le fasi di un processo produttivo sono automatizzabili allo stesso grado e che il ruolo del lavoratore è in essi ineliminabile.
Moody, soprattutto, non coglie la stretta relazione che vi è tra innovazioni organizzative (Lean Production) e innovazioni tecnologiche (Industria 4.0). Dalle inchieste che ho fatto è emerso come siano proprio le tecnologie 4.0 a rendere pienamente implementabili alcuni principi della Lean Production. Per questo trovo poco condivisibile la frase, “le aziende abbandonano i metodi snelli a favore della tecnologia digitale”. Per due ragioni. La prima: io sto vedendo l’esatto contrario: con la diffusione delle tecnologie 4.0 sono parecchie le aziende che hanno avviato o, per quelle che erano già su questa strada, che hanno sviluppato modelli di Lean Production. La seconda: cosa vuol dire “tecnologie digitali”? Queste non sono collocate in uno spazio etereo, privo di materialità, ma al contrario innervano proprio i materialissimi processi di produzione: quali tecnologie digitali si potrebbero utilizzare in una fabbrica senza robot, macchinari, impianti automatizzati, magazzini logistici, dispositivi individuali (tablet ecc.) assegnati al “pickerista”, al preparatore di kit di assemblaggio, alla singola postazione di lavoro ecc.? La connettività è il cuore di Industria 4.0: si tratta di un sistema nervoso che attraversa l’intero processo produttivo, comprese – e per certi versi soprattutto – le fasi materiali di esso.
Quindi, a mio parere, ben difficilmente appare possibile: a) riscontrare nella realtà concreta un abbandono generalizzato della Lean Production; b) introdurre una separazione tra innovazioni tecnologiche e organizzative, quando invece le stesse sono più intrecciate tra loro; c) isolare le “tecnologie digitali” sia dal contesto tecnologico esistente (robot, macchinari ecc.) che da quello organizzativo.
Altri sono gli aspetti discutibili. Moody afferma: “Gli spedizionieri si sono rivolti a conservare più scorte”. È possibile, ma:
1) Come sono misurati? Con quali dati? Poiché non sembra riferirsi a dati di Contabilità Nazionale, forse trae questa affermazione dai dati relativi alle scorte (giacenze) dei bilanci aziendali? Anche in questo caso è possibile, ma non va dimenticato che in contabilità aziendale essi possono essere oggetto di variazioni di natura monetaria: per esempio da una parte le svalutazioni tramite gli opportuni Fondi; oppure risentire dei diversi metodi utilizzati (FIFO, LIFO ecc.). Ad esempio a parità di volumi, e in presenza di incremento dei prezzi di quei prodotti/materiali (cosa assai verosimile in fasi di inflazione significativa), l’applicazione del metodo FIFO fa lievitare il valore di un magazzino;
2) siamo sicuri che nel passato tali scorte fossero proprio così basse – prossime al famoso “zero scorte” – come prescrivono i principi della Lean? Ho i miei dubbi. Indubbiamente c’è stata una pressione alla riduzione del magazzino, ma va anche ricordato che alcune imprese utilizzatrici di componenti/materiali si tutelavano dalla possibile mancanza/ritardo di tali input attraverso la tecnica del Consignment Stock, con i fornitori che garantivano un determinato livello di giacenze presso il magazzino del cliente (in conto deposito) e questo che prelevava i quantitativi necessari al suo ciclo produttivo, con cadenze variabili (anche giornaliere).
Moody richiama una survey di Accenture del 2023 condotta su oltre 1.200 aziende, secondo la quale “il 42 per cento era già passato dal Jit al sourcing multiplo e il 72 per cento prevedeva di farlo entro tre anni”. Francamente non mi sembra una novità che le imprese utilizzino più fornitori per lo stesso tipo di componentistica. Questo può avvenire per ridurre il rischio di mancate/ritardate forniture, o per mettere i fornitori in competizione tra loro. Ma ripeto: non mi sembra una novità così dirompente, anzi. Non mi convince nemmeno l’implicita sovrapposizione tra Just in Time e mono-fornitura: tale strumento organizzativo si basa sulla sincronizzazione delle forniture (in questo caso stiamo parlando della rete esterna all’impresa/stabilimento presa in considerazione), a prescindere dal numero di fornitori del medesimo componente/materiale.
Infine Moody sembra assumere un approccio analitico un po’ limitativo quando scrive: “L’importanza del Jit è stata la riduzione dei costi delle scorte, sia di componenti che di prodotti finiti”. Il Just in Time non è finalizzato solo, e nemmeno soprattutto, a questo; quanto piuttosto a evitare i fenomeni di “sovrapproduzione”, che nella logica Lean sono indice di “sprechi”, cioè di impiego di un eccesso di lavoro rispetto a quello corrispondente al livello degli ordini acquisiti per quel particolare periodo temporale. Un eccesso di lavoro – il contrario della “fabbrica minima” – potrebbe tradursi in dissaturazioni nelle postazioni di lavoro, riducendo carichi e ritmi di lavoro, riducendo così la produttività, cioè l’estrazione di plusvalore relativo.
——————————————————————————
Il 2 maggio scorso, la statunitense Labor Notes pubblicava un articolo di Kim Moody, uno dei fondatori della rivista e dei più attenti osservatori del mondo del lavoro, intitolato “The End of Lean Production…and What’s Ahead”. Jacobin Italia lo ha tradotto (“Oltre la produzione snella” ) e lo ha messo online l’11 maggio (Oltre la produzione snella – Jacobin Italia) e ci ha concesso l’utilizzo della traduzione da loro pubblicata. La presentiamo qui, corredata dei commenti di Sergio Fontegher Bologna, Bruno Cartosio, Matteo Gaddi, Romeo Orlandi e Marco Veruggio che ne discutono affermazioni e implicazioni da angolazioni diverse. L’insieme verrà pubblicato anche su: www.puntocritico.info
Kim Moody, Oltre la produzione snella
Sergio Fontegher Bologna, La produzione snella e il governo della logistica
Bruno Cartosio, La distribuzione è vulnerabile
Matteo Gaddi, Commento a “Oltre la produzione snella” di Kim Moody
Romeo Orlandi, Note su “Oltre la produzione snella” di Kim Moody